طراح در طراحی و ساخت یک ماشین چند قطعه را در کنار هم قرار می دهد. ماشین مونتاژ شده باید بتواند انتظارطراح را برای برآورده کردن هدف خاصی دنبال کند. شکل و اندازه های اجزای سازنده ی این ماشین نقشی اساسی در توفیق طراح می تواند داشته باشد. این اندازه ها معمولاً به وسیله محاسبه و یا طبق تجربه طراح تعیین می شود. آگاهی از نقش قطعه در مکانیسم مورد نظر، تعیین نیروهای وارده در ضمن عملکرد، محاسبه تنش های وارده، اعمال یک ضریب اطمینان معقول و شرایط کاربرد از جمله عواملی هستند که در تعیین اندازه و ابعاد قطعه موثر هستند. اندازه ای که با توجه به این موارد گفته شده به دست می آید همان اندازه دقیق قطعه است. در صنعت رسیدن به اندازه ی دقیق با توجه به سختی قطعه، استهلاک ماشین ابزار، خطاهای اندازه گیری و غیره امکان پذیر نیست. همه قطعات و سطوح یک مجموعه نیاز به یک دقت فوق العاده در اندازه نداشته و بر حسب نوع کاری که هر سطح از یک قطعه انجام می دهد درجه دقت آن نیز فرق می کند. به همین دلایل مفهوم تلرانس (Tolerance) مطرح می شود. برای اطمینان از خوب سوار شدن قطعات قابل تعویض یک ماشین و کارکرد صحیح آن، طراح معمولاً انحراف های مجاز از اندازه ی اسمی ابعاد قطعه را بر روی نقشه ی آن قید می کند. این انحرافات را تلرانس می گویند. اختلاف بین ماکزیمم و مینیمم یک کمیت بیانگر مفهوم تلرانس است.
برای ساختن هر قطعه در صنعت سه اندازه باید در نظر گرفته شود:
- اندازه اسمی (Nominal Size or Basic Size): یعنی اندازه ای که بر روی نقشه نوشته می شود.
- اندازه ماکزیمم (Upper Limit of Size) یا ULS: یعنی بزرگ ترین اندازه قطعه و به عبارت دیگر اندازه ای که در موقع ساختن نباید از آن تجاوز نمود.
- اندازه مینیمم (Lower Limit of Size) یا LLS: یعنی کمترین اندازه ی قابل قبول قطعه.
مقدار تلرانس برابر است با تفاوت کوچک ترین و بزرگ ترین اندازه قابل قبول قطعه. این مفاهیم در شکل زیر نشان داده شده است.

محدوده تلرانس بین اندازه های حداقل و حداکثر است. خط صفر با اندازه اسمی مطابق و برای حدود بالا و پایین به عنوان خط مبنا تلقی می شود.
به مثال شکل های زیر دقت کنید:

دقت تا آنجا لازم است که طراح آن را مشخص کرده است. اگر تلرانس زیاد باشد هزینه و زمان ساخت پایین است ولی از نظر مرغوبیت زیاد عالی نیست. بر عکس ساخت قطعه ای که تلرانس آن کم است مشکل تر بوده ولی مرغوب تر است.

مفهوم انطباقات:
بر حسب نوع درگیری قطعات در یک ماشین، انطباق (Fit) مطرح می شود. وقتی دو قطعه در داخل یکدیگر قرار می گیرند، گفته می شود آن دو قطعه بر هم منطبق شده اند یا یک انطباق به وجود آورده اند. در یک تعریف، اگر دو قطعه تلرانس دار در یکدیگر قرار گیرند (محور یا میله و سوراخ)، رابطه بین اندازه خارجی یک محور (میله) و اندازه داخلی سوراخی که در هم مونتاژ می شوند را انطباق می گویند. در یک انطباق، سطوحی با یکدیگر مجاور خواهند شد که لازمه ی این مجاورت، تداخل به هر شکلی است. این سطوح را سطوح انطباقی می گویند. منظور از محور یا میله در یک انطباق، قطعه ای است که وارد قطعه دیگر (سوراخ) می شود. محور یا میله علاوه بر شکل عمومی خود که استوانه است، در این مفهوم می تواند هر شکل و فرمی را شامل شود. منظور از سوراخ در یک انطباق هم قطعه ای است که یک قطعه دیگر وارد آن می شود. پس به طور کلی یک اندازه خارجی را محور یا میله و یک اندازه داخلی را سوراخ می گویند.
انواع انطباق:
اندازه های انطباقی محور (میله) و سوراخ می توانند سه حالت را در انطباق با هم به وجود آورند که عبارتند از:
- انطباق آزاد یا بازی دار یا لقی دار (Clearance Fit):
در انطباق آزاد قطعات می توانند نسبت به هم جابجا شوند. مثلاً جهت به دست آوردن انطباق آزاد برای محوری که باید در داخل یک سوراخ قرار بگیرد کافی است قطر محور از سوراخ کمتر باشد. تفاضل اندازه های دو قطعه را آزادی و حداکثر مقدار آن را که عبارت از اختلاف مابین بزرگ ترین قطر سوراخ و کوچک ترین قطر محور است لقی می گویند. انطباق های آزاد متعددی بر حسب مقدار لقی و خصوصیات حالات ساخت قطعات وجود دارد که نوع هر یک با سرعت دورانی میله، میزان روغن زنی، درجه گرم کردن طول سطح در تماس با آن ارتباط دارد. مفهوم انطباق آزاد در شکل زیر نشان داده شده است.

- انطباق پرسی یا فشاری (Interference Fit):
در انطباق پرسی دو قطعه نمی توانند به سادگی درگیر شوند زیرا قطر محور کمی بزرگ تر از قطر سوراخ است، لذا محور را باید به کمک نیروی قابل ملاحظه ای در سوراخ فرو برد. مثلاً با دستگاه پرس هر دو را می توان تحت فشار قرار داد. قطعه سوراخ دار را حرارت داد تا بر قطر آن افزوده شود و یا اینکه محور را سرد کرد تا قطر آن تقلیل یابد. مفهوم انطباق پرسی در شکل زیر نشان داده شده است.

- انطباق عبوری یا روان یا انتقالی (Transition Fit):
در این انطباق، قطعات ضمن نداشتن لقی در یکدیگر قابل حرکت و لغزیدن با نیروی کم هستند. مفهوم انطباق عبوری در شکل زیر نشان داده شده است.

در شکل زیر این سه نوع انطباقات با هم نشان داده شده است:

سیستم های انطباقی:
تعیین اندازه های خارجی محور و اندازه های داخلی سوراخ در هر یک از انطباق ها به دو روش یا سیستم یا دستگاه انجام می شود که معمولاً با در نظر گرفتن همه شرایط به ویژه موجود بودن ابزارهای استاندارد صورت می گیرد. این سیستم های انطباقی عبارتند از:
- سیستم انطباقی سوراخ مبنا (Hole-Basis Fit System):
در این سیستم ابتدا اندازه سوراخ آماده می شود و سپس اندازه محور با آن هماهنگ می شود. پس در این سیستم اندازه حداقل سوراخ ثابت و با اندازه اسمی برابر است و قطر محور را طوری تغییر می دهند تا انواع انطباقات حاصل شود. در واقع محورها به اندازه مقدار لقی یا اضافه اندازه لازم کوچک تر یا بزرگ تر از سوراخ ها هستند. در این سیستم انحراف تحتانی را صفر می گیرند. به این روش سیستم ثبوت سوراخ هم می گویند. از سیستم انطباقی ثبوت سوراخ معمولاً در صنایع سبک مثل ماشین سازی، خودرو سازی و محدوده های تولیدی که در آن ها محورهای پله دار باید با یاتاقان ها، چرخ ها، کوپلینگ ها و غیره کوپل شوند استفاده می شود. محورها را آسان تر و با ابزار کمتر نسبت به سوراخ ها می توان به اندازه انطباقی مورد نظر رساند. مفهوم سیستم انطباقی سوراخ مبنا در شکل زیر نشان داده شده است.

- سیستم انطباقی محور (میله) مبنا (Shaft-Basis Fit System):
در این سیستم ابتدا اندازه محور آماده می شود و سپس اندازه سوراخ با آن هماهنگ می شود. پس در این سیستم اندازه حداکثر محور ثابت و با اندازه اسمی برابر است و اندازه سوراخ را طوری تغییر می دهند تا انواع انطباقات حاصل شود. در واقع سوراخ ها به اندازه مقدار لقی یا اضافه اندازه لازم کوچک تر یا بزرگ تر از محور ها هستند. در این سیستم انحراف فوقانی را صفر می گیرند. به این روش سیستم ثبوت محور هم می گویند. از سیستم انطباقی ثبوت سوراخ معمولاً در صنایع سنگین مثل ساختمان ماشین های کشاورزی، ماشین های نساجی، ساخت قطعات نوار نقاله و محدوده های تولیدی که در آن ها محورهای بلند با قطر یکسان تولید می شوند، استفاده می شود. محورها را آسان تر و با ابزار کمتر نسبت به سوراخ ها می توان به اندازه انطباقی مورد نظر رساند. مفهوم سیستم انطباقی محور مبنا در شکل زیر نشان داده شده است.

در شکل های زیر انواع انطباق در دو سیستم انطباقی محور مبنا و سوراخ مبنا نشان داده شده است:


سه حالت انطباق در سیستم سوراخ مبنا

سه حالت انطباق در سیستم محور مبنا
رده تلرانس:
وقتی جفت شدن دو قطعه برای مقصودی معین و انطباق آن ها مد نظر باشد، تنها اطلاع از نوع انطباق کافی نیست و باید موقعیت تلرانس محور و سوراخ نسبت به یک مبنا (خط صفر) و مقدار عددی آن ها مشخص باشد. در استاندارد ایزو برای مشخص کردن این موقعیت و مقدار تلرانس از یک علامت شامل حرف و عدد به عنوان رده تلرانسی استفاده شده است (شکل زیر).

این مشخصه جایگزین سیستم های انطباقی کشورهای مختلف شده و یک علامت مشترک و همه فهمی را به عنوان رده تلرانسی برای محور و سوراخ و علامت انطباقی در مونتاژ آن دو معرفی کرده است. در واقع طبق این سیستم، سوراخ ها و محورها توسط سازنده های مختلف با موقعیت های تلرانسی معین و مورد قبول اکثر کشورها ساخته می شوند تا از مشکلات انطباق و مونتاژ پیشگیری شود.
در رده تلرانسی ایزو، مفهوم موقعیت تلرانس نشان دهنده حد پایینی انحراف از اندازه اسمی یا به عبارت دیگر کوچک ترین فاصله محدوده یا میدان تلرانس از خط صفر (خط مبنا) است. برای نشان دادن این موقعیت در مورد سوراخ ها یا اندازه های داخلی از حروف لاتین بزرگ و در مورد محورها یا اندازه های خارجی از حروف لاتین کوچک استفاده می شود. شکل زیر حرف مربوط به موقعیت تلرانس برای سوراخ و محور را مشخص کرده است.

طبق جداول شکل فوق، موارد زیر باید مورد توجه باشد:
- حرف H برای سوراخ و h برای محور به عنوان موقعیت مبنا یا خط صفر در نظر گرفته شده است. در موقعیت H، کوچک ترین اندازه سوراخ برابر با اندازه اسمی است، یعنی انحراف پایینی برابر صفر است. در موقعیت h، بزرگ ترین اندازه محور برابر با اندازه اسمی است، یعنی انحراف بالایی برابر صفر است.
- هر قدر فاصله محدوده یا میدان تلرانس از خط صفر زیادتر باشد حروف بزرگ یا کوچکی که در مورد سوراخ یا محور به کار می رود باید از حروف H یا h در الفبا بیشتر دور باشد.
- برای یک سوراخ 10 موقعیت برای اندازه های بزرگ تر از اندازه اسمی (از A تا G) مشخص شده است. این موقعیت ها برای انطباق آزاد یا بازی دار است. در موقعیت G، کمترین انحراف و در موقعیت A بیشترین انحراف از خط مبنا وجود دارد. در واقع، با ثابت بودن اندازه محور، در موقعیت G کمترین لقی و در موقعیت A بیشترین لقی وجود دارد.
- به عبارت خیلی ساده، با حرکت از موقعیت G به A، سوراخ نسبت به اندازه اسمی بزرگ تر ساخته می شود. به عنوان مثال اگر اندازه اسمی سوراخ 20 باشد، اندازه سوراخ در موقعیت G مثلاً 0.06+20 و در موقعیت A مثلاً 0.09+20 است.
- برای یک سوراخ 17 موقعیت برای اندازه های کوچک تر از اندازه اسمی (از J تا ZC) مشخص شده است. این موقعیت ها برای انطباق های پرسی یا فشاری و عبوری است. در موقعیت J، کمترین انحراف و در موقعیت ZC بیشترین انحراف از خط مبنا وجود دارد. در واقع با ثابت بودن اندازه محور، مونتاژ در موقعیت ZC نیاز به نیروی فشاری بیشتری دارد.

- به عبارت خیلی ساده، با حرکت از موقعیت J به ZC، سوراخ نسبت به اندازه اسمی کوچک تر ساخته می شود. به عنوان مثال اگر اندازه اسمی سوراخ 20 باشد، اندازه سوراخ در موقعیت J مثلاً 0.06-20 و در موقعیت ZC مثلاً 0.09-20 است.
- برای یک محور یا میله 10 موقعیت برای اندازه های کوچک تر از اندازه اسمی (از a تا g) مشخص شده است. این موقعیت ها برای انطباق آزاد یا بازی دار است. در موقعیت g، کمترین انحراف و در موقعیت a بیشترین انحراف از خط مبنا وجود دارد. در واقع، در موقعیت g، لقی کمترین و در موقعیت a لقی بیشترین مقدار را دارد.
- به عبارت خیلی ساده، با حرکت از موقعیت g به a، محور نسبت به اندازه اسمی کوچک تر ساخته می شود. به عنوان مثال اگر اندازه اسمی محور 20 باشد، اندازه سوراخ در موقعیت g مثلاً 0.06-20 و در موقعیت a مثلاً 0.09-20 است.
- برای یک سوراخ 17 موقعیت برای اندازه های بزرگ تر از اندازه اسمی (از j تا zc) مشخص شده است. این موقعیت ها برای انطباق های پرسی یا فشاری و عبوری است. در موقعیت j، کمترین انحراف و در موقعیت zc بیشترین انحراف از خط مبنا وجود دارد. در واقع با ثابت بودن اندازه سوراخ، مونتاژ در موقعیت ZC نیاز به نیروی فشاری بیشتری دارد.
- به عبارت خیلی ساده، با حرکت از موقعیت j به zc، محور نسبت به اندازه اسمی بزرگ تر ساخته می شود. به عنوان مثال اگر اندازه اسمی محور 20 باشد، اندازه سوراخ در موقعیت j مثلاً 0.06+20 و در موقعیت zc مثلاً 0.09+20 است.
برای درک بهتر این مفاهیم به شکل های زیر توجه کنید:


علاوه بر موقعیت تلرانس، مقدار آن نیز در رده تلرانسی ذکر می شود. مقدار تلرانس در استاندارد ISO، با درجه ی تلرانس استانداردی برای محدوده اندازه های اسمی مختلف تعریف شده است. این درجه های تلرانس استاندارد، به دلیل تاثیر بر دقت و کیفیت ساخت، کیفیت انطباق را هم مشخص می کند. استاندارد ISO برای نشان دادن درجه های تلرانس استاندارد یا کیفیت و ردیف تلرانس، از ترکیب عبارت IT (مخفف ISO Tolerance) به همراه یک عدد استفاده می کند. در سلسله انطباقات ایزو، 20 کیفیت برای تلرانس در نظر گرفته شده است. این 20 کیفیت عبارتند از:
IT01, IT0, IT1, IT2, IT3, … , IT17, IT18
هر چه عدد همراه با IT کوچک تر باشد، محدوده تلرانس کمتر و اندازه نسبی دقیق تر خواهد بود. کیفیت های IT5 تا IT11 کیفیت های متوسط برای کارهای دقیق هستند و برای انطباقات متداول در صنعت استفاده می شوند. کیفیت های IT12 تا IT18 در تلرانس های خشن و تلرانس های تولیدی بزرگ مثل ابزارآلات نورد و حدیده ها و کیفیت های IT01 تا IT4 در تلرانس کارهای خیلی دقیق مثل شابلون ها، ابزارهای اندازه گیری و اندازه های خیلی حساس استفاده می شود.
در حال حاضر در استاندارد ایزو، تا اندازه اسمی 3150 میلی متر، 21 محدوده اندازه اسمی طبق جدول زیر معرفی شده است.

برای هر یک از این 21 محدوده، 20 کیفیت یا درجه تلرانس استاندارد تعریف شده است. برای هر یک از این 20 کیفیت تلرانسی، مقدار محدوده تلرانس برای هر محدوده اندازه اسمی در جدول بالا مشخص شده است. برای مثال برای IT7، مقدار تلرانس اندازه اسمی 20 میلی متر برابر 21 میکرون است. محدوده تلرانس برای این اندازه اسمی 20 هم بر اساس موقعیت تلرانس مشخص می شود. برای مثال اگر یک سوراخ با اندازه اسمی 20 در موقعیت H ساخته شود، به دلیل اینکه موقعیت H بر اندازه اسمی منطبق است، کوچک ترین اندازه سوراخ همان 20 و بزرگ ترین اندازه آن 0.021+20 خواهد بود. این حالت را به صورت 20H7 نشان می دهند. همچنین اگر یک محور با اندازه اسمی 20 در موقعیت h ساخته شود، به دلیل اینکه موقعیت h بر اندازه اسمی منطبق است، بزرگ ترین اندازه محور همان 20 و کوچک ترین اندازه آن 0.021-20 خواهد بود. این حالت را به صورت20h7 نشان می دهند.
برای موقعیت های انطباقی مختلف، محدوده تلرانس یا حد بالا و پایین اندازه برای سوراخ و محور در استاندارد ISO 286-2 آمده است. این استاندارد را می توانید از لینک زیر در عصر مواد دریافت کنید.
2010 : ISO 286-2
برای فهم بهتر مطالب به مثال های زیر توجه کنید:
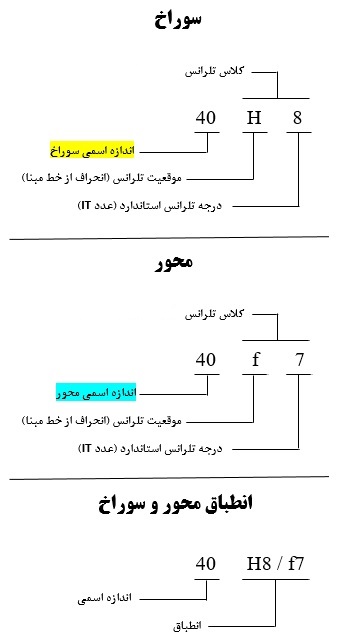
برای انطباق 40H8/f7، محدوده تلرانس محور و سوراخ به صورت زیر است:
تلرانس سوراخ:
موقعیت انطباقی H بر خط مبنا قرار می گیرد یعنی انحراف پایینی سوراخ برابر صفر است. از جدول زیر، مقدار محدوده تلرانس IT8 برای اندازه 40 برابر 39 میکرون است، یعنی انحراف بالایی سوراخ برابر 0.039+40 است. پس حد پایینی تلرانس اندازه سوراخ 40 و حد بالایی تلرانس آن 40.039 است.

تلرانس محور:
موقعیت انطباقی f از نوع آزاد است. طبق جدول زیر، مقدار محدوده تلرانس IT7 برای اندازه 40 برابر 25 میکرون است. حال برای مشخص کردن اندازه حد بالا و پایین به جداول معرفی شده در استاندارد ISO 286-2 مراجعه می کنیم. برش مورد نظر ما از جداول این استاندارد در ادامه مطلب نشان داده شده است. طبق این جدول، انحراف پایینی و بالایی محور از اندازه اسمی به ترتیب 0.050- و 0.025- است. پس مقدار حد پایینی تلرانس اندازه این محور 39.950 و مقدار حد بالایی تلرانس آن 39.975 است.


|
امتیاز مطلب : 2
|
تعداد امتیازدهندگان : 1
|
مجموع امتیاز : 1